FRP Replaces Secondary Steel & Lowers Embodied Carbon of Data Centers
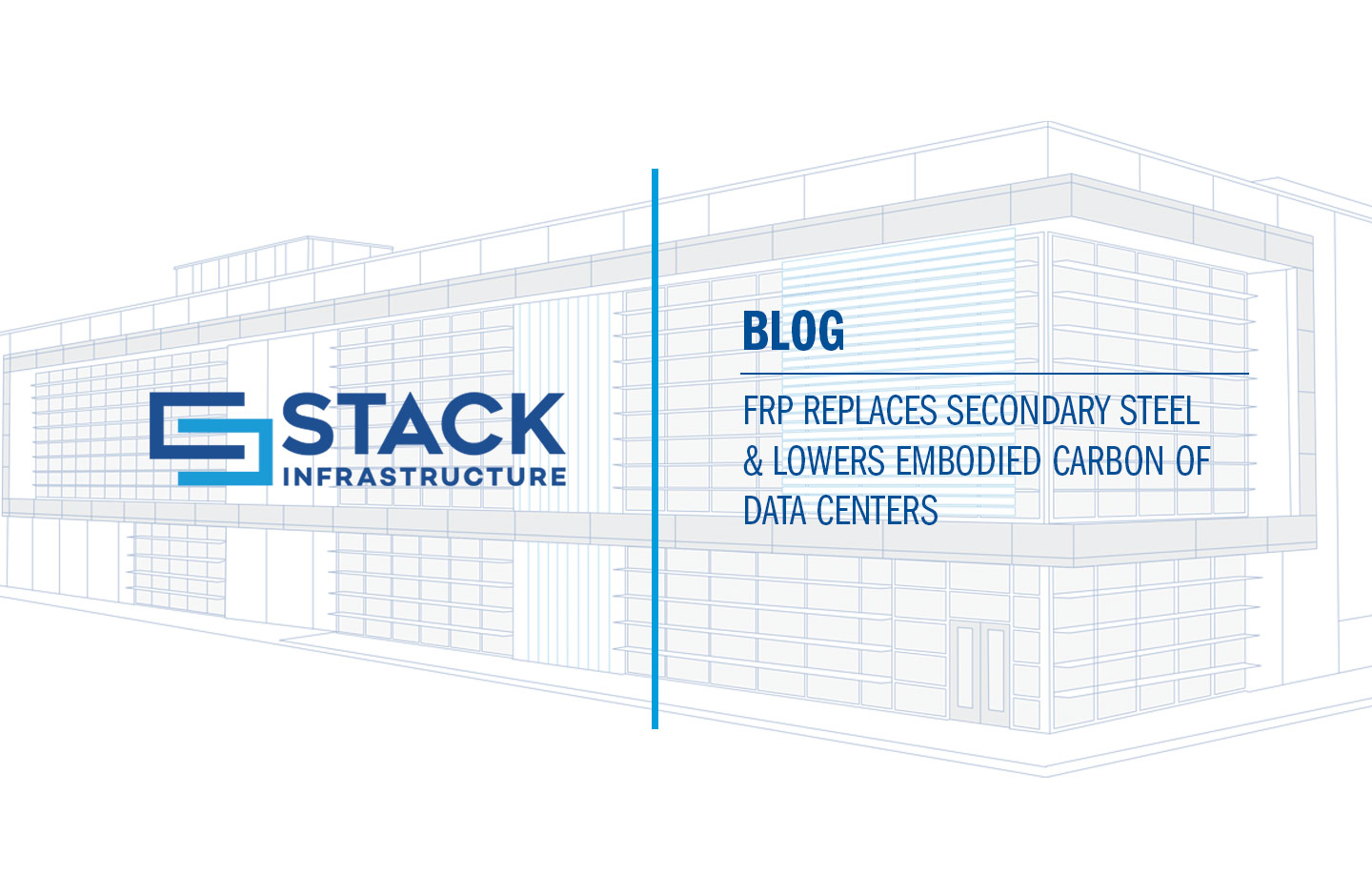
Each year the world produces enough steel to build an Eiffel Tower every three minutes—that’s 180,000 Eiffel Towers per revolution of the sun—and while the Eiffel Tower is made of iron, not steel, it makes for a good visual analogy.
As a crucial building material in both commercial and residential construction, steel production has increased tenfold since 1950. In 2021, global steel production reached 1.95 billion tons, to which the United States attributed over 85 million. Currently, the production of one ton of steel requires approximately twenty gigajoules of energy. Coal has traditionally been a key part of the steel-making process, and it is estimated that 1.85 tons of carbon dioxide is released for every ton of steel created. That means steel production in 2021 emitted over 3.6 billion tons of carbon dioxide into the atmosphere.
Steel is a primary building material for industries across the world, and its use may never be fully eliminated from construction. Nevertheless, steel alternatives and mixed material designs can help significantly reduce the embodied carbon of structures. One such steel alternative is fiber reinforced polymer (FRP). For several years, STACK Infrastructure has been working with technology partner, Advantic Building Group, to capitalize on FRP’s carbon, weight, and cost savings that positively impact production time and safety within STACK’s data center development. STACK has been able to reduce the overall use of steel by supplementing the secondary steel package with FRP for items such as screen walls and access platforms, positively impacting our carbon footprint.
Secondary Steel Substitute
Pultruded FRP structural profiles feature a composite structural system primarily composed of 65-75% continuous fibers encased within 25-35% polyester resin. The fiber strands form continuous rovings that are bonded together in a specific orientation to optimize strength and stiffness. The resin is not only a binding agent but also provides corrosion, UV, and impact resistance along with increased durability. The composite material boasts a high strength-to-weight ratio, which allows for the use of less material and a resulting lower embodied carbon total than steel structures.
Due to numerous inherent material advantages, fiber reinforced composites have been used in construction since the 1990s, and yet, steel has remained the traditionally preferred building material with 57 tons of steel used every second throughout 2018. However, with governments and clients demanding action on climate change mitigation, more industries are beginning to take advantage of FRP’s lower rate of carbon emissions.
Due to its strength-to-weight ratio, FRP over secondary steel has a weight savings of approximately 40-75%, depending on the system being supported. The degree of weight savings impacts the level of carbon reduction. As a result, the utilization of FRP instead of secondary steel has shown to reduce a structure’s embodied carbon nearly 60-85%.
For hyperscalers and large enterprises aiming to reduce their embodied carbon and achieve their sustainability goals, FRP is a valuable building material that offers various benefits in addition to reduced environmental impact within data center development.
Capitalizing on the Advantages of FRP over Steel in Construction
FRP’s high strength-to-weight ratio generates a waterfall of rewards for data center developers.
Shipping cost and sustainability
- FRP weighs 80% less than steel, which allows for trucks to carry more at once, reducing the number of trucks and the amount of fuel needed. Trucking of structural shapes can decrease 30 to 60%, depending on the size of the structure.
Fewer Cranes
- Cranes are only utilized for primary picks during rooftop installations, and individual sections can be hand carried to final destinations.
Reduced Embodied Carbon
- In addition to releasing fewer carbon emissions during production than steel, FRP further decreases its total embodied carbon due to the abovementioned advantages of fewer trucks and cranes and their resulting emissions.
No Welding
- Since all FRP connections are bolted, welding is eliminated, saving on specialized labor and tools.
Elimination of Grounding
- There is no need for grounding to safely redirect electricity. Skipping this step means fewer laborers, less cost, and a faster schedule.
Improved Safety
- The eradication of welding also improves safety, removes risk of sparks or fire, and reduces chance of injury. Reducing the number of crane picks aids in the reduction of safety risk for the sites as well.
Smaller Crew
- The benefits of FRP, including less weight, fewer cranes, no welding, and no grounding, simplify the installation process. Craftmanship crew sizes could shrink 25 to 30%. Fewer skill requirements also bring access to a wider pool of available talent.
Faster Timeline
- Eliminating the need for extra equipment or time for additional processes generally speeds up the production schedule. Raw materials continue to experience long lead times due to supply chain issues. Steel can take 20 to as many as 32 weeks, while FRP ranges from 12 to 16 weeks.
Increased Productivity
- The speed and ease of installing FRP often leads to 4x the overall productivity in comparison to sites utilizing steel for secondary packages.
Cost Reduction
- Advantages such as fewer laborers, less processes, and faster timelines ultimately contribute savings to the overall cost of construction, often decreasing it by 10-20%.
Little to No Corrosion
- While steel corrodes over the course of its lifecycle, FRP is resistant to a broad range of chemicals.
Overcoming the Setbacks of FRP as a Steel Alternative
Certain characteristics impede FRP’s usage as a primary building material and allow it to replace only secondary steel packages.
Combustible Material
- FRP has an ASTM E-84 Class 1 flame spread rating. While it will not add fuel to the fire, FRP will singe locally within flames; but once the flames are pulled away, it will self-extinguish. It will continue to hold load in a fire; however, since it is deemed a combustible material, FRP will not be utilized as a primary structural material. Data centers with fire suppression systems may safely use FRP in secondary packages.
Heat Constraints
- For environments over 150° Fahrenheit, steel or mixed material designs are better solutions than FRP due to its heat constraints. However, data centers generally do not get above 150° F, and therefore, FRP can be safely used.
Deflection
- FRP is 1/10th the elastic modulus of steel which typically results in a deeper beam profile to achieve the same deflection performance under the same loading and span. Typically, bracing is utilized to limit system drift and member deflection. Depending on the application, layout, and loading of the structure, dual material designs can be designed to utilize steel in isolated locations (i.e. long spans, critical frames/connections) with FRP being deployed for the majority of secondary members.
Sand Shortage
- Glass is a primary ingredient in FRP. Composed from sand, glass production contributes to the annual global usage of 50 billion tons of sand, which is the second-most exploited natural resource. To help combat the sand shortage, production of FRP will eventually shift to recycled glass. Additionally, European researchers are actively investigating methods of repurposing wind turbine blades and recycling their glass FRP composite materials. Such technology will eventually translate over into the United States.
While FRP cannot be used as a primary material, secondary FRP can help reduce the amount of primary steel needed and, ultimately, decrease a data center’s embodied carbon.
A Steely-Eyed Look at the Status of Steel Alternatives in Data Centers
Annual global steel production generates enough Eiffel Towers that, if they were positioned side by side, would wrap from Paris to New York three and a half times. With 1.85 tons of carbon dioxide released for every ton of steel produced, it is critical that industries around the world decrease their steel usage as much as possible.
Steel alternative fiber reinforced polymer and designs mixing both steel and FRP can help significantly reduce the embodied carbon of structures. Not only does the production of FRP generate less carbon emissions, but FRP’s strength-to-weight ratio also allows for less trucking, rigging, welding, and grounding and, thus, lowers overall Scope 3 emissions. Additionally, FRP’s requirements for less assembling, less crew members, and less specialized talent increases productivity, reduces safety risks, cuts costs, and speeds timelines.
FRP should be integrated into the design and engineering of data centers early in the development process to reduce the amount of primary steel needed. STACK actively collaborates with technology partner Advantic Building Group to continually improve the usage of secondary FRP in our data centers. Over the last three years, STACK has increased the amount of FRP in our secondary steel packages, beginning with screen walls and moving on to generator platforms and structural framing on brownfield sites. Next, STACK will be exploring this steel alternative for dunnage, stairs, crossover ladders, conduit support, and more in our efforts to shrink our overall carbon footprint and support client sustainability goals.
Primary steel may not disappear from industrial production for some time, but in the meantime, digital infrastructure developers can increase their usage of secondary FRP to deliver more sustainable data centers.
By Tin Fong, Vice President, Energy & Sustainability, and Rick Waddle, SVP, Development
October 13, 2022
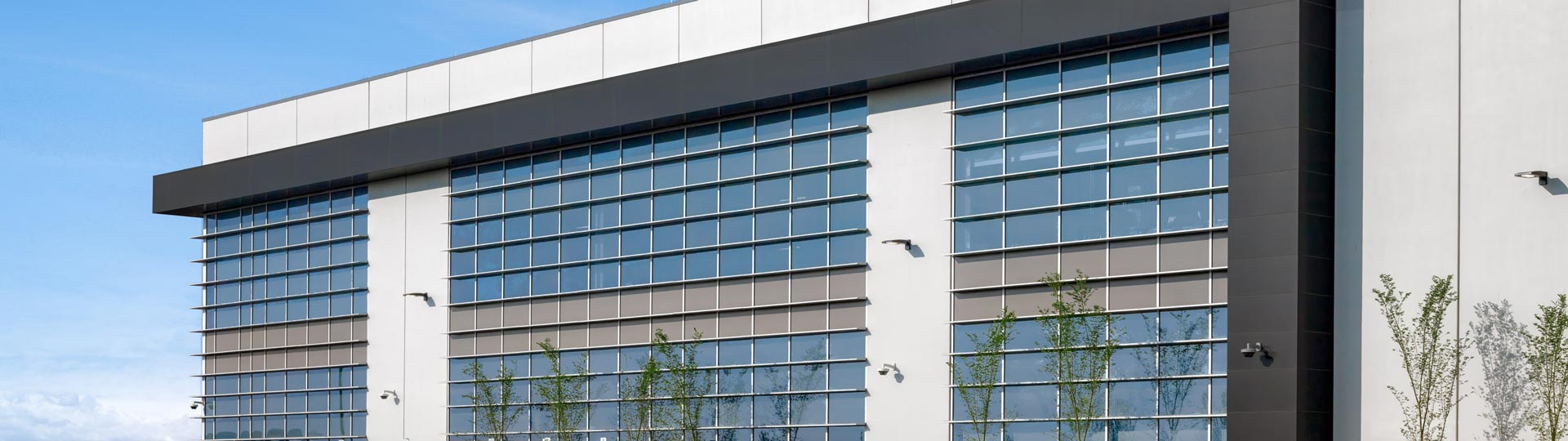